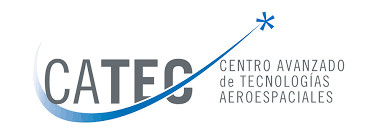
NOTA DE PRENSA
TECNOLOGÍA ESPAÑOLA RUMBO A JÚPITER: EL CATEC Y CITD FABRICAN LOS COMPONENTES EN ALUMINIO MÁS GRANDES HASTA LA FECHA MEDIANTE IMPRESIÓN 3D PARA UNA SONDA ESPACIAL
• La nave espacial JUICE (JUpiter ICy moons Explorer) se pondrá en órbita de manera inminente e iniciará un viaje espacial de 8 años hasta llegar a su destino y objetivo: explorar el complejo entorno del planeta Júpiter y sus satélites Ganimedes, Europa y Calisto.
• Esta misión de la Agencia Espacial Europea cuenta con la tecnología del Centro Avanzado de Tecnologías Aeroespaciales (CATEC) y la empresa de ingeniería española CiTD, que han fabricado 11 componentes estructurales mediante fabricación aditiva metálica (impresión 3D) consiguiendo una reducción de peso del 52% respecto de sus versiones desarrolladas por tecnología convencional, clave en la optimización de la estructura de la nave espacial.
Sevilla, 13 de abril de 2023. La primera misión europea con destino al planeta Júpiter estará en órbita de manera inminente. Comenzará entonces un viaje de 8 años que tiene el objetivo de explorar el planeta gigante gaseoso del Sistema Solar y sus lunas gélidas Ganimedes, Europa y Calisto, en busca de agua líquida.
Pero este viaje se inició hace varios años, cuando más de 80 entidades europeas pusieron al servicio de la Agencia Espacial Europea su tecnología más puntera para desarrollar la sonda espacial JUICE (JUpiter ICy moons Explorer). Entre ellas, la empresa de ingeniería CiTD y el Centro Avanzado de Tecnologías Aeroespaciales (CATEC), que han aunado esfuerzos y recursos para superar conjuntamente uno de los retos propuestos en esta misión espacial: reducir el peso de la estructura secundaria de la nave JUICE aplicando la tecnología de fabricación aditiva metálica en las 11 piezas que se han fabricado desde nuestro país. “Este es realmente un gran hito para la industria espacial europea, y sin duda para el CATEC, donde hemos desarrollado los soportes de los sensores de misión y de otros mecanismos de actuación, que si bien pertenecen a la estructura secundaria de la nave JUICE son críticos para la misión. Hemos conseguido una reducción de peso del 52% respecto de las soluciones desarrolladas por tecnología de fabricación convencional”, señala el Dr. Fernando Lasagni, Director Técnico de Materiales y Procesos de CATEC.
El proceso utilizado para la fabricación de estos componentes ha sido la fundición por láser en cama de polvo, y que básicamente consiste en un láser de alta potencia que funde, capa a capa, partículas de polvo metálico y generando un cuerpo sólido. Gracias a la libertad de diseño que permite esta tecnología se pueden generar geometrías que pesan entre un 30 y un 60 por ciento menos en masa.
TECNOLOGÍA ESPAÑOLA RUMBO A JÚPITER: EL CATEC Y CITD FABRICAN LOS COMPONENTES EN ALUMINIO MÁS GRANDES HASTA LA FECHA MEDIANTE IMPRESIÓN 3D PARA UNA SONDA ESPACIAL
• La nave espacial JUICE (JUpiter ICy moons Explorer) se pondrá en órbita de manera inminente e iniciará un viaje espacial de 8 años hasta llegar a su destino y objetivo: explorar el complejo entorno del planeta Júpiter y sus satélites Ganimedes, Europa y Calisto.
• Esta misión de la Agencia Espacial Europea cuenta con la tecnología del Centro Avanzado de Tecnologías Aeroespaciales (CATEC) y la empresa de ingeniería española CiTD, que han fabricado 11 componentes estructurales mediante fabricación aditiva metálica (impresión 3D) consiguiendo una reducción de peso del 52% respecto de sus versiones desarrolladas por tecnología convencional, clave en la optimización de la estructura de la nave espacial.
Sevilla, 13 de abril de 2023. La primera misión europea con destino al planeta Júpiter estará en órbita de manera inminente. Comenzará entonces un viaje de 8 años que tiene el objetivo de explorar el planeta gigante gaseoso del Sistema Solar y sus lunas gélidas Ganimedes, Europa y Calisto, en busca de agua líquida.
Pero este viaje se inició hace varios años, cuando más de 80 entidades europeas pusieron al servicio de la Agencia Espacial Europea su tecnología más puntera para desarrollar la sonda espacial JUICE (JUpiter ICy moons Explorer). Entre ellas, la empresa de ingeniería CiTD y el Centro Avanzado de Tecnologías Aeroespaciales (CATEC), que han aunado esfuerzos y recursos para superar conjuntamente uno de los retos propuestos en esta misión espacial: reducir el peso de la estructura secundaria de la nave JUICE aplicando la tecnología de fabricación aditiva metálica en las 11 piezas que se han fabricado desde nuestro país. “Este es realmente un gran hito para la industria espacial europea, y sin duda para el CATEC, donde hemos desarrollado los soportes de los sensores de misión y de otros mecanismos de actuación, que si bien pertenecen a la estructura secundaria de la nave JUICE son críticos para la misión. Hemos conseguido una reducción de peso del 52% respecto de las soluciones desarrolladas por tecnología de fabricación convencional”, señala el Dr. Fernando Lasagni, Director Técnico de Materiales y Procesos de CATEC.
El proceso utilizado para la fabricación de estos componentes ha sido la fundición por láser en cama de polvo, y que básicamente consiste en un láser de alta potencia que funde, capa a capa, partículas de polvo metálico y generando un cuerpo sólido. Gracias a la libertad de diseño que permite esta tecnología se pueden generar geometrías que pesan entre un 30 y un 60 por ciento menos en masa.
Soporte de rueda de reacción de la sonda espacial JUICE
Unas geometrías que serían imposibles de fabricar utilizando otras técnicas de mecanizado convencionales. Esta tecnología ha sido aplicada por CATEC, junto con CiTD y AIRBUS, en el desarrollo de once piezas altamente optimizadas en Aluminio Al-Mg-Sc (Scalmalloy®). En palabras de Marta García-Cosio, Directora de CiTD, “la misión espacial JUICE requiere una gran reducción en masa de la estructura frente a los instrumentos científicos y al combustible, y gracias a la tecnología de impresión 3D hemos podido diseñar y optimizar la masa de la estructura secundaria del satélite”.
El reto no solo ha sido fabricar los componentes en aluminio más grandes hasta la fecha mediante impresión 3D para una sonda espacial, sino hacerlo en tiempo record. La fabricación de estos componentes requieren tiempos que van desde 24 horas hasta 5 días, en el caso de los elementos de mayor tamaño. Previa a la fabricación, se diseñó un plan detallado de ensayos para la caracterización dinámica y estática del comportamiento mecánico de la aleación de aluminio empleada, así como para validar otros aspectos relativos a la conductividad térmica y eléctrica del material. En paralelo, y teniendo en cuenta las exigencias del proyecto, se ha desarrollado un método de monitorización de la materia prima fabricación, controlando aspectos como la composición química de la aleación entre otros aspectos, y la fiabilidad de los sistemas de fabricación. Al final de la fabricación, se han aplicado los métodos más revolucionarios de inspección, recurriendo a la tomografía computerizada, método que permite asegurar la máxima calidad de cada uno de los componentes.
CATEC lleva trabajando en la tecnología de impresión 3D para el sector espacial desde el año 2011, y ha participado en la fabricación de la estructura crítica para satélites de telecomunicaciones o de exploración como QUANTUM, PROBA3 y CHEOPS, este último también con CiTD. “Esta experiencia adquirida ha sido clave para que la Agencia Espacial Europea confíe en CATEC para esta histórica misión espacial a Júpiter, un reto también para nosotros que ha marcado un antes y un después en nuestro centro tecnológico”, afirma el Dr. Lasagni.
Sobre el Centro Avanzado de Tecnologías Aeroespaciales (CATEC)
CATEC es un centro tecnológico avanzado que contribuye a la mejora de la competitividad de las empresas del sector aeroespacial mediante la investigación e innovación tecnológica, la creación de conocimiento, la transferencia de tecnología y los servicios avanzados. Gestionado por la Fundación Andaluza para el Desarrollo Aeroespacial (FADA), cuenta con una plantilla compuesta por más de 80 especialistas y técnicos. En sus diez años de trayectoria, se ha convertido en uno de los centros tecnológicos más activos en proyectos de I+D+i nacional y europea, destacándose en campos como el desarrollo de tecnologías y aplicaciones de fabricación avanzada e Industria 4.0, los sistemas aéreos no tripulados o drones (UAS/RPAS), la inteligencia artificial, entre otros. Actualmente trabaja en más de 60 proyectos de I+D, tanto con organismos públicos de investigación como con empresas, liderando en varios de ellos iniciativas de los programas europeos como Horizonte Europa, Interreg y Clean Aviation de la Comisión Europea, y en varios programas promovidos por la Agencia Espacial Europea.
Sobre CiTD
CiTD Engineering & Technologies es una empresa española nacida en 2015 partiendo de la sólida unidad productiva de la empresa ITD, líder en la industria Aeroespacial y de Defensa, de la cual hereda toda su experiencia y tecnología. CiTD ofrece soluciones de ingeniería de diseño y análisis, para sistemas y componentes estructurales del sector aeroespacial principalmente, y posterior diversificación a sectores como la energía y las infraestructuras. La profesionalidad y dedicación de una plantilla de cerca de 50 ingenieros y especialistas, así como la estrategia de invertir en nuevas tecnologías, con su apuesta por la impresión 3D, le ha permitido posicionarse como una de las empresas españolas más activas en el desarrollo de piezas de vuelo en el sector espacial.
Para más información:
Gabinete de Prensa de CATEC
Celia Ruiz (+34) 654 74 64 73
cruiz@euromediagrupo.es
Descarga de nota de prensa y fotos
Unas geometrías que serían imposibles de fabricar utilizando otras técnicas de mecanizado convencionales. Esta tecnología ha sido aplicada por CATEC, junto con CiTD y AIRBUS, en el desarrollo de once piezas altamente optimizadas en Aluminio Al-Mg-Sc (Scalmalloy®). En palabras de Marta García-Cosio, Directora de CiTD, “la misión espacial JUICE requiere una gran reducción en masa de la estructura frente a los instrumentos científicos y al combustible, y gracias a la tecnología de impresión 3D hemos podido diseñar y optimizar la masa de la estructura secundaria del satélite”.
El reto no solo ha sido fabricar los componentes en aluminio más grandes hasta la fecha mediante impresión 3D para una sonda espacial, sino hacerlo en tiempo record. La fabricación de estos componentes requieren tiempos que van desde 24 horas hasta 5 días, en el caso de los elementos de mayor tamaño. Previa a la fabricación, se diseñó un plan detallado de ensayos para la caracterización dinámica y estática del comportamiento mecánico de la aleación de aluminio empleada, así como para validar otros aspectos relativos a la conductividad térmica y eléctrica del material. En paralelo, y teniendo en cuenta las exigencias del proyecto, se ha desarrollado un método de monitorización de la materia prima fabricación, controlando aspectos como la composición química de la aleación entre otros aspectos, y la fiabilidad de los sistemas de fabricación. Al final de la fabricación, se han aplicado los métodos más revolucionarios de inspección, recurriendo a la tomografía computerizada, método que permite asegurar la máxima calidad de cada uno de los componentes.
CATEC lleva trabajando en la tecnología de impresión 3D para el sector espacial desde el año 2011, y ha participado en la fabricación de la estructura crítica para satélites de telecomunicaciones o de exploración como QUANTUM, PROBA3 y CHEOPS, este último también con CiTD. “Esta experiencia adquirida ha sido clave para que la Agencia Espacial Europea confíe en CATEC para esta histórica misión espacial a Júpiter, un reto también para nosotros que ha marcado un antes y un después en nuestro centro tecnológico”, afirma el Dr. Lasagni.
Sobre el Centro Avanzado de Tecnologías Aeroespaciales (CATEC)
CATEC es un centro tecnológico avanzado que contribuye a la mejora de la competitividad de las empresas del sector aeroespacial mediante la investigación e innovación tecnológica, la creación de conocimiento, la transferencia de tecnología y los servicios avanzados. Gestionado por la Fundación Andaluza para el Desarrollo Aeroespacial (FADA), cuenta con una plantilla compuesta por más de 80 especialistas y técnicos. En sus diez años de trayectoria, se ha convertido en uno de los centros tecnológicos más activos en proyectos de I+D+i nacional y europea, destacándose en campos como el desarrollo de tecnologías y aplicaciones de fabricación avanzada e Industria 4.0, los sistemas aéreos no tripulados o drones (UAS/RPAS), la inteligencia artificial, entre otros. Actualmente trabaja en más de 60 proyectos de I+D, tanto con organismos públicos de investigación como con empresas, liderando en varios de ellos iniciativas de los programas europeos como Horizonte Europa, Interreg y Clean Aviation de la Comisión Europea, y en varios programas promovidos por la Agencia Espacial Europea.
Sobre CiTD
CiTD Engineering & Technologies es una empresa española nacida en 2015 partiendo de la sólida unidad productiva de la empresa ITD, líder en la industria Aeroespacial y de Defensa, de la cual hereda toda su experiencia y tecnología. CiTD ofrece soluciones de ingeniería de diseño y análisis, para sistemas y componentes estructurales del sector aeroespacial principalmente, y posterior diversificación a sectores como la energía y las infraestructuras. La profesionalidad y dedicación de una plantilla de cerca de 50 ingenieros y especialistas, así como la estrategia de invertir en nuevas tecnologías, con su apuesta por la impresión 3D, le ha permitido posicionarse como una de las empresas españolas más activas en el desarrollo de piezas de vuelo en el sector espacial.
Para más información:
Gabinete de Prensa de CATEC
Celia Ruiz (+34) 654 74 64 73
cruiz@euromediagrupo.es
Descarga de nota de prensa y fotos
El Dr. Fernando Lasagni, Director Técnico de Materiales y Procesos de CATEC, y Marta García-Cosio, Directora de CiTD


